Do This To Optimize Picking Accuracy

6 Ways To Improve Picking Accuracy Falcon Fulfillment How to optimize order picking accuracy. improving order picking accuracy doesn’t have to be expensive, or even complicated. here are some simple strategies for optimizing order picking accuracy that you can implement in your operations. organize your warehouse or fulfillment center. chaos can cause a lot of problems, especially in picking. Continuous improvement and feedback loop. improving warehouse picking speed and accuracy hinges on a cycle of order feedback and refinement. the key lies in listening to the order pickers, analyzing order performance data, and embracing lean principles to streamline the order process.
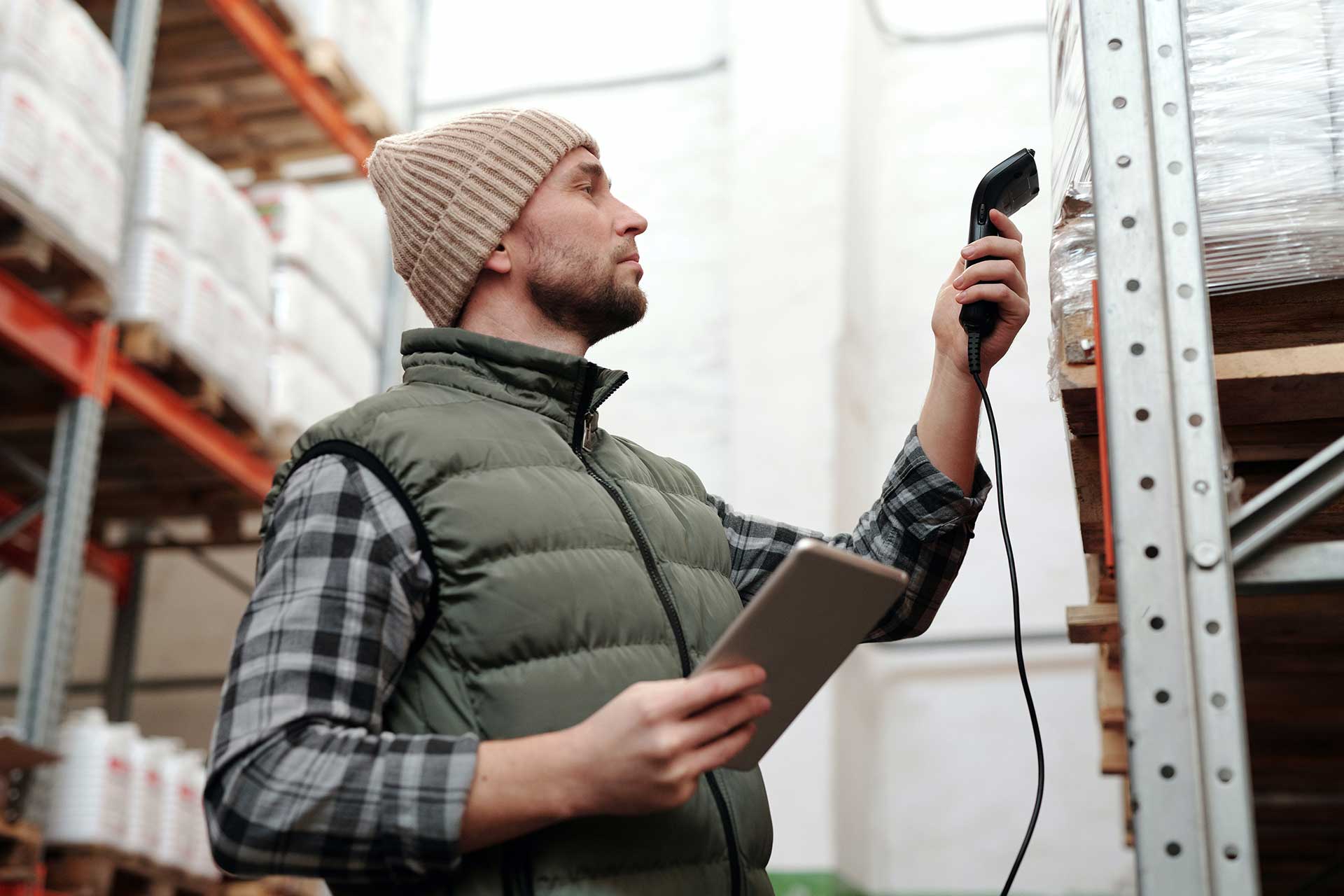
6 Ways To Improve Order Picking Accuracy Falcon Fulfillment Measure order picking accuracy. order picking accuracy is number three on the most important benchmarks for warehouses in 2020’s dc measures benchmarking report. a low order picking accuracy points to a need for more efficient processes, better control standards, more in depth training and more. The picking rate measures how many items are picked per hour. it can be tracked at the order level, indicating the time taken to pick a complete order by using the following calculation: picking rate = total picks. total time spent. according to warehousing and fulfillment, the average of the industry is around 71 items per hour which is a good. Problem 1: wrong item location in warehouse. this occurs when a picker goes to the warehouse location to pick an order, and the correct item is not there. if an item is not where it should be in the warehouse, this means the picker needs to spend time looking for it. this delays the order fulfillment, which can lead to an unhappy customer and. To summarize, barcode scanning is a cost effective way to improve warehouse picking accuracy by minimizing manual errors, providing real time tracking and enhancing the overall efficiency of warehouse picking operations. 2. double down on quality control. quality control checks are key to improving the accuracy of your warehouse picking operation.
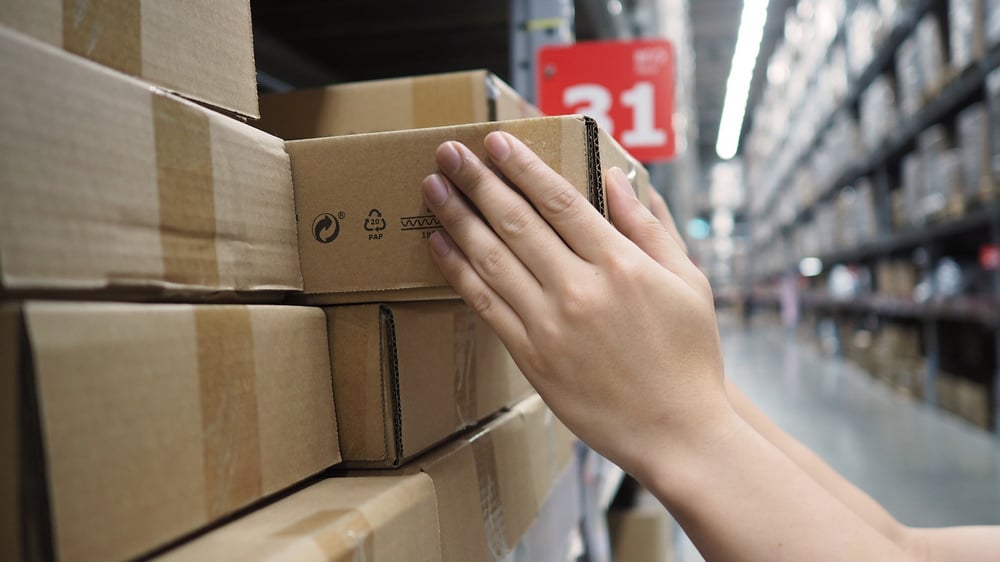
5 Ways To Improve Picking Accuracy In Your Warehouse Problem 1: wrong item location in warehouse. this occurs when a picker goes to the warehouse location to pick an order, and the correct item is not there. if an item is not where it should be in the warehouse, this means the picker needs to spend time looking for it. this delays the order fulfillment, which can lead to an unhappy customer and. To summarize, barcode scanning is a cost effective way to improve warehouse picking accuracy by minimizing manual errors, providing real time tracking and enhancing the overall efficiency of warehouse picking operations. 2. double down on quality control. quality control checks are key to improving the accuracy of your warehouse picking operation. Therefore, we have prepared a list of best practices to reduce errors during the picking process. 1. implement a barcode scanning system across the warehouse. a barcode scanning system can drastically reduce fulfillment errors by electronically transmitting data tied to skus or purchase orders. Establish picking routes. creating clear picking routes or establishing a streamlined traffic flow within the warehouse allows pickers to fulfill orders seamlessly. this minimizes backtracking through aisles, reducing both costs and time. overcrowded aisles are also alleviated by the implementation of well defined picking routes.
Comments are closed.