Mrl Compresor Discharge And Cooling Lubrication System Diagram

Compressor Lubrication Best Practices Page 1 industrial air compressor ls 10 25, 30 & 40 hp 18, 22 & 30 kw standard & 24 kt operator’s manual and parts list keep for future reference part number 02250105 114 esullair corporation page 2 air care seminar training sullair air care seminars are 3 day courses that provide hands on instruction in the proper operation. 26 6.3 compressor air inlet system 28 6.4 compressor cooling and lubrication system water cooled 30 6.5 compressor unit tubing 34 6.6 compressor cooling and lubrication system air cooled 38 6.7 compressor discharge system 42 6.8 electro pneumatic control system 44 6.9 sullicon control 46 6.10 instrument panel assembly.
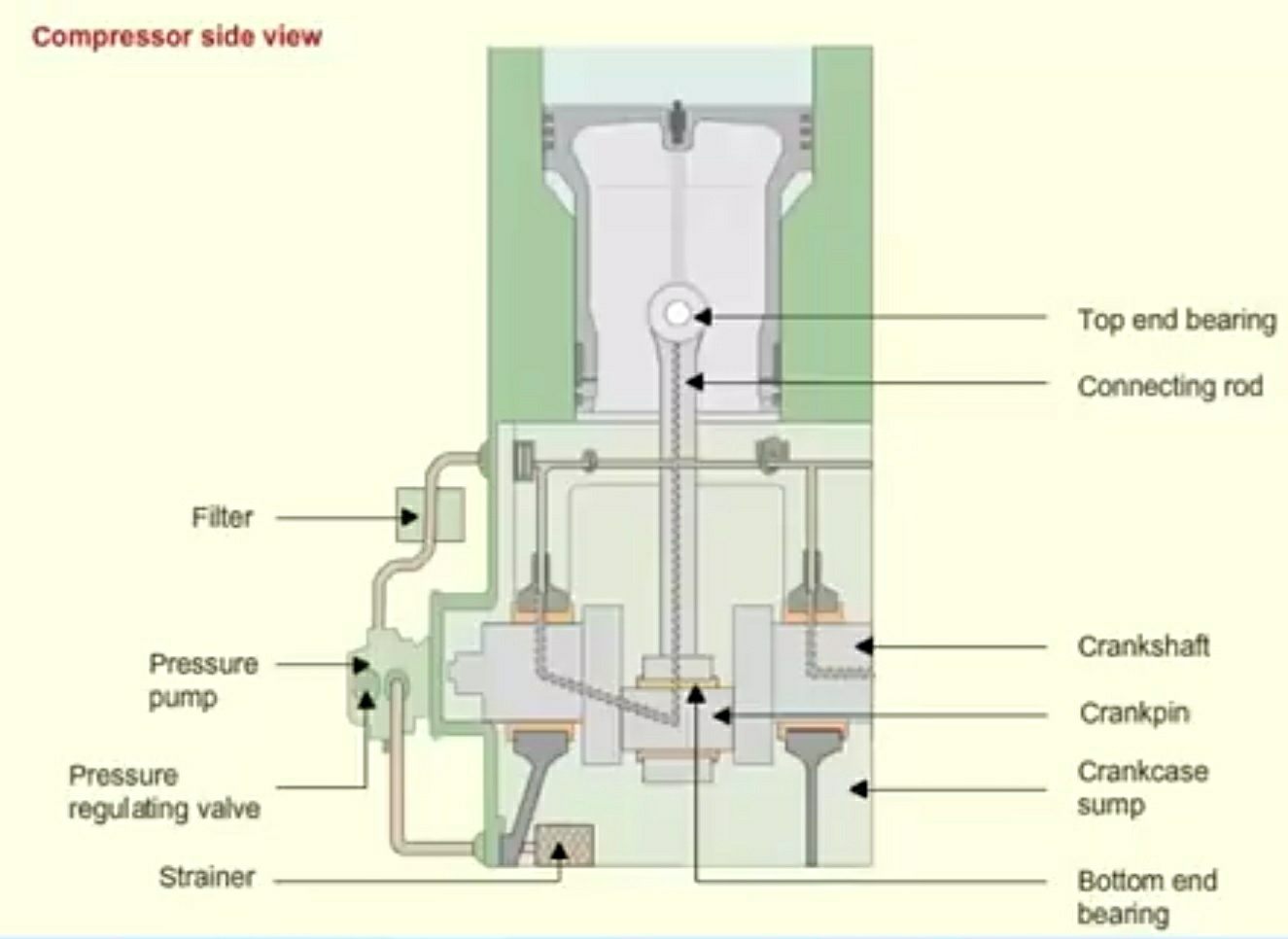
Lubrication System For Air Compressor Marine Engineers Knowledge Page 14 section 2 description figure 2 3 compressor cooling and lubrication and discharge system (water cooled) page 15 100 psig (6.9 bar). as a result, the differential pressure all sullair compressor models are equipped with a regulator for the spiral valve gradually opens apply high pressure shutdown switch to shut down the ing air. Check the pressure gauge reading on reservoir and wait until reservoir pressure drops to approximately 0.5bar (7psig). close the 1 4 turn valve on the blow down valve. remove the drain plug and attach the 1 4 npt barb fitting and drain tube (supplied with the unit) to the drain on the oil air separator tank. The 3700 series compressors are factory filled with sullube lubricant. for more information on fluid fill, consult section 3, specifications. sullair 24kt compressors are filled with a fluid that rarely needs to be changed. use only sullair 24kt fluid in the event that a fluid change is required. Connect the compressor to the plant air system with a flexible connector rated for at least 200 psi (1380 kpa) and 275° f (135° c). support the piping to insure that no pipe stress is transmitted to any compressor component. compressor should be piped into a receiver tank prior to any filters or dryer.

Compressor Lubrication Best Practices The 3700 series compressors are factory filled with sullube lubricant. for more information on fluid fill, consult section 3, specifications. sullair 24kt compressors are filled with a fluid that rarely needs to be changed. use only sullair 24kt fluid in the event that a fluid change is required. Connect the compressor to the plant air system with a flexible connector rated for at least 200 psi (1380 kpa) and 275° f (135° c). support the piping to insure that no pipe stress is transmitted to any compressor component. compressor should be piped into a receiver tank prior to any filters or dryer. This article deals with the lubrication of dynamic compressors (figure 1). figure 1. compressor key components. dynamic compressors have a few key components that require a coolant lubricant: gears, bearings and seals. to date, the majority of dynamic compressors continue to utilize oil film lubricated seals, as illustrated in figures 2d, 3a. 3.3 motor. the electric motor used to power each sullivan palatek ud series 125 250 horsepower compressor is a nema special inverter duty 3 phase motor, fitted with a c face register at the compressor drive end to assure proper coupling alignment at all times. the main compressor motor is connectable for 460 volts.
Compressor Package Lubrication Oil System Matlab Simulink This article deals with the lubrication of dynamic compressors (figure 1). figure 1. compressor key components. dynamic compressors have a few key components that require a coolant lubricant: gears, bearings and seals. to date, the majority of dynamic compressors continue to utilize oil film lubricated seals, as illustrated in figures 2d, 3a. 3.3 motor. the electric motor used to power each sullivan palatek ud series 125 250 horsepower compressor is a nema special inverter duty 3 phase motor, fitted with a c face register at the compressor drive end to assure proper coupling alignment at all times. the main compressor motor is connectable for 460 volts.

Compressor Lubrication Best Practices
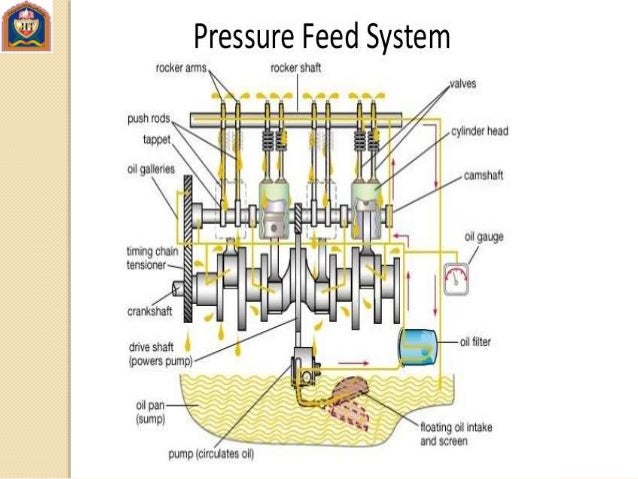
Cooling And Lubrication System
Comments are closed.